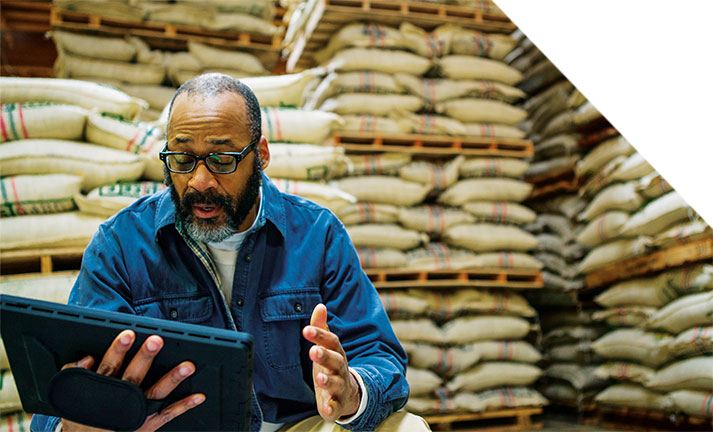
08 Jun Slow moving inventory and stock reduction in international company with Microsoft Dynamics NAV
In global companies it is possible to effectively reduce the slow moving inventory in multiple warehouses. Slow moving inventory in one warehouse may be required in other subsidiary. If a group of companies starts collecting data about those products, there is a good chance of stock reduction in their global quantity.
Having access to reports on slow moving inventory, Subsidiary D purchases the required item from Subsidiary B, which enables stock redution from the group perspective
A list of slow moving stock in the group warehouses
When a Subsidiary D is in need of a given item, as shown in the figure below, it may turn out that the item is available in warehouses in other subsidiary (in this case Subsidiary B). If the group of companies uses Master Data Management System for ERP solution, it is possible to create in the central database a special list of slow moving items in the warehouses including information about their quantities.
The process of collecting data defining slow moving inventory
The process is not fully automatic and there must one employee at the headquarters supervising the whole procedure. The problem is that it is hard to adopt one single standard, according to which ERP system Microsoft Dynamics NAV could automatically classify slow moving inventory (e.g. based on how long they linger in the warehouse). Some items may be needed in a given subsidiary even though they had been stored in its warehouse for a long time. The person managing the process at the headquarters must monitor the inventory in individual subsidiaries on a regular basis and determine which items should be added to the list of slow moving stock. For example, headquarters employee selected 10 slow moving items that, in his opinion, should be placed on the list. After consultation with the subsidiary it turned out that 2 items were still needed by the sellers and 3 other items would probably be sold soon. Ultimately, only 5 items could be added to the list.
Slow moving inventory reminder during ordering
Once the list of slow moving inventory is complete, a report in MS Excel file is created and placed in the central database. It is then forwarded to all subsidiaries, for example on a monthly basis. The report may be useful when a subsidiary places an order for a given item. If it is found in the report, ERP system (in this case Microsoft Dynamics NAV – Navision) will automatically display a warning message with a list of other locations in which the item is available. The message appears because every time a purchase order is entered, ERP system (Microsoft Dynamics NAV) checks whether the ordered item can be found in the report.
Possibility to ignore the message
Obviously, in companies, in which the discussed solution was implemented, it was possible to ignore the message and purchase the item even though it was a slow moving inventory in other warehouse. However, the strategy of most companies – the stock reduction – remains the same.
Replenishment optimization
Store replenishment is a similar example. The system searches slow moving inventory and suggests moving them to subsidiaries which need them.
One more case I would like to mention concerns a company which faced a problem before implementing the solution for managing inventory in multiple warehouses. The company managed to negotiate with the vendor the possibility of returning the products lingering in the store. However, after the first return of the product, the vendor inquired how some of the stores return the item while others order the same item.